
The role of aluminum extrusion heat sinks as exterior components with colored surface treatments
Aluminum extrusion heat sinks with colored surface treatments serve multiple critical roles as exterior components in various applications, combining functional performance with aesthetic and environmental benefits. Below is a detailed analysis of their key roles:
1. Extursion Heat Sink Efficient Heat Dissipation
![]() | ![]() | ![]() |
- Dark-colored coatings (e.g., black anodizing) increase solar absorptivity, which may be beneficial in applications requiring heat retention (e.g., solar thermal systems).
- Light-colored coatings (e.g., white powder coating) reduce solar heat gain, making them suitable for outdoor electronics or lighting fixtures in high-temperature environments, as they minimize heat absorption from sunlight.
2. Extursion Heat Sink Aesthetic Enhancement
- Customizable finishes: Processes like anodizing, powder coating, or electrophoretic painting allow vibrant, durable colors (e.g., metallic hues, matte textures, or even wood-grain effects) to match branding, building facades, or outdoor landscapes.
- Architectural applications: In exterior building systems (e.g., solar panels, LED lighting fixtures, or ventilation systems), colored heat sinks can blend seamlessly with the structure’s design, enhancing visual harmony rather than appearing as industrial afterthoughts.
- Product differentiation: In consumer electronics (e.g., outdoor speakers, security cameras), colored heat sinks contribute to a product’s unique identity, appealing to design-conscious users.
3. Extursion Heat Sink Corrosion and Weather Resistance
- Anodizing: Creates a thick aluminum oxide layer (up to 25 microns) that resists corrosion, UV fading, and abrasion. Colored anodizing integrates dye into the oxide layer for long-lasting colorfastness.
- Powder coating: A polymer-based coating applied electrostatically and cured at high temperatures, offering excellent resistance to chipping, fading, and chemical exposure. It is ideal for harsh climates (e.g., coastal areas, industrial zones).
- Electroplating or PVD (Physical Vapor Deposition): Thin metallic coatings (e.g., chrome, nickel) add corrosion resistance and decorative finishes, though they are less commonly used for large extrusions due to cost
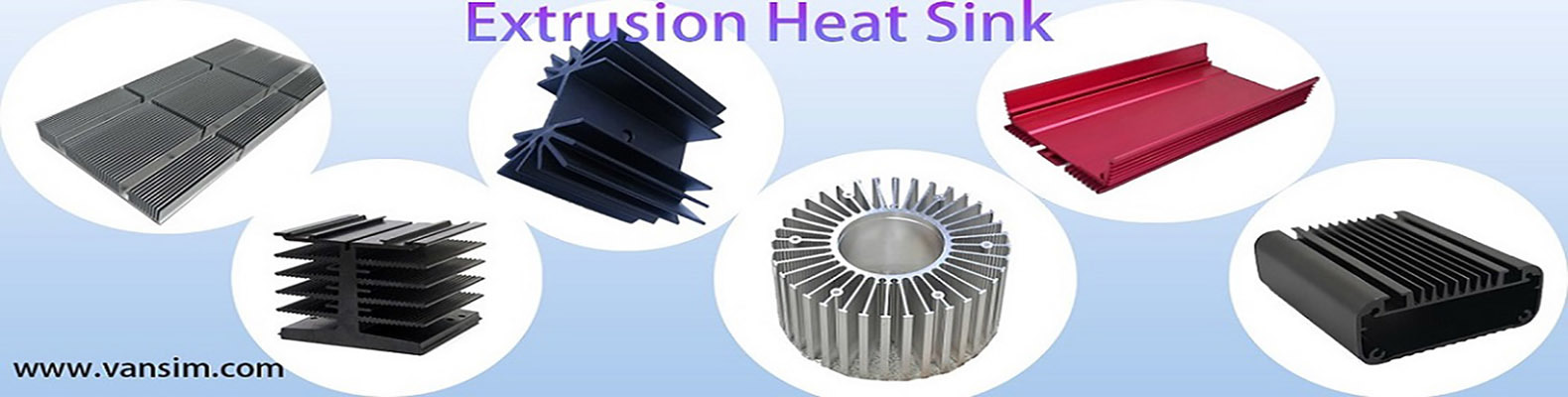
4.Extursion Heat Sink Environmental and Functional Adaptability
- Solar control: Light-colored coatings with high solar reflectance (SRI) reduce the "urban heat island" effect in building applications by reflecting sunlight, lowering the heat sink’s temperature and adjacent ambient air.
- UV stability: Specialized coatings (e.g., fluoropolymer-based powders) resist degradation from prolonged UV exposure, ensuring color and performance longevity in outdoor settings.
- Anti-graffiti or self-cleaning coatings: In public spaces, heat sinks can be treated with superhydrophobic or anti-adhesive layers, combining color with functional maintenance benefits.
5. Extursion Heat Sink Structural and Installation Benefits
- Lightweight strength: Aluminum is significantly lighter than copper or steel, reducing structural load and installation costs for large-scale projects (e.g., outdoor signage, stadium lighting).
- Design flexibility: Extrusion allows complex fin geometries (e.g., straight, serrated, or pin fins) tailored to airflow requirements, while colored treatments can be applied uniformly across intricate shapes.
- Modular systems: Colored heat sinks can be pre-fabricated as standardized modules, enabling quick assembly and replacement in field applications.
6. Extursion Heat Sink Sustainability and Recyclability
Extursion Heat Sink Applications Examples
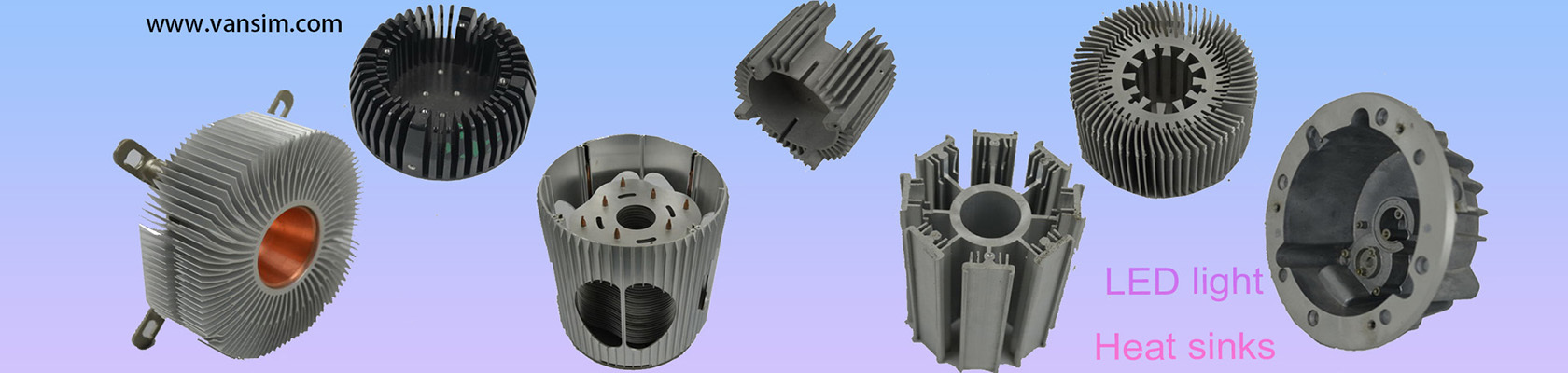
Extursion Heat Sink Challenges and Considerations
- Color vs. Thermal Performance: Dark colors enhance heat absorption, which may be undesirable in some applications (e.g., cooling electronics). Engineers must balance aesthetic goals with thermal requirements using computational fluid dynamics (CFD) modeling.
- Coating Adhesion: Proper pretreatment of aluminum (e.g., degreasing, etching) is critical to ensure coatings bond securely and resist peeling or flaking.
- Regulatory Compliance: In some markets, exterior components must meet standards for fire resistance, weathering, or energy efficiency (e.g., LEED certification), influencing coating and material choices.
Conclusion

Aluminum Extrusion heat sink
Contact Us
Classification